The heart is the engine of the body, typically beating at a rate of 60 to 100 beats per minute. But what happens when your heart can’t keep up?
A pacemaker is a crucial element to helping regulate a cardiac patient’s natural electrical system, correcting the heartbeat when it is too slow or irregular. There are two primary parts of a pacemaker: the pulse generator, which controls the rate of electric pulses along with a battery; and the lead wires that deliver the pulses to the heart. The lead wires are placed directly into the chambers of the heart to adjust the heartrate through the electric pulses.
Lead wires are inserted into a vessel near the collar bone to make their way to the heart. On one end, they are connected to the pacemaker. The other end sits in one or multiple chambers of the heart. Earlier versions of pacemaker lead wires would need to be replaced after ten years of round-the-clock performance, these wires would need to be replaced, requiring another surgery and the possibility of complications.
At the time, ATI 35N™ alloy was the best choice as it was resistant to corrosion and high strength, but it included a lot of titanium which, in this application, fatigued too quickly. After flexing and operating within the human body for about 10 years, the former alloy could not keep up, resulting in the need to replace the lead wires. With the human life expectancy increasing, this meant more extraction and insertion surgeries for patients potentially resulting in scar tissue, chances for infection, and even long-term nerve damage. A new material was essential to increase the quality of life for cardiac patients.
Fort Wayne Metals—manufacturer of medical grade wire— had long been a partner with ATI. Now, they came with a challenge. How can we build a wire that is corrosion and fatigue resistant, but still conductive in order to carry a charge to the heart. Together the companies developed a new alloy: 35N LT®*.
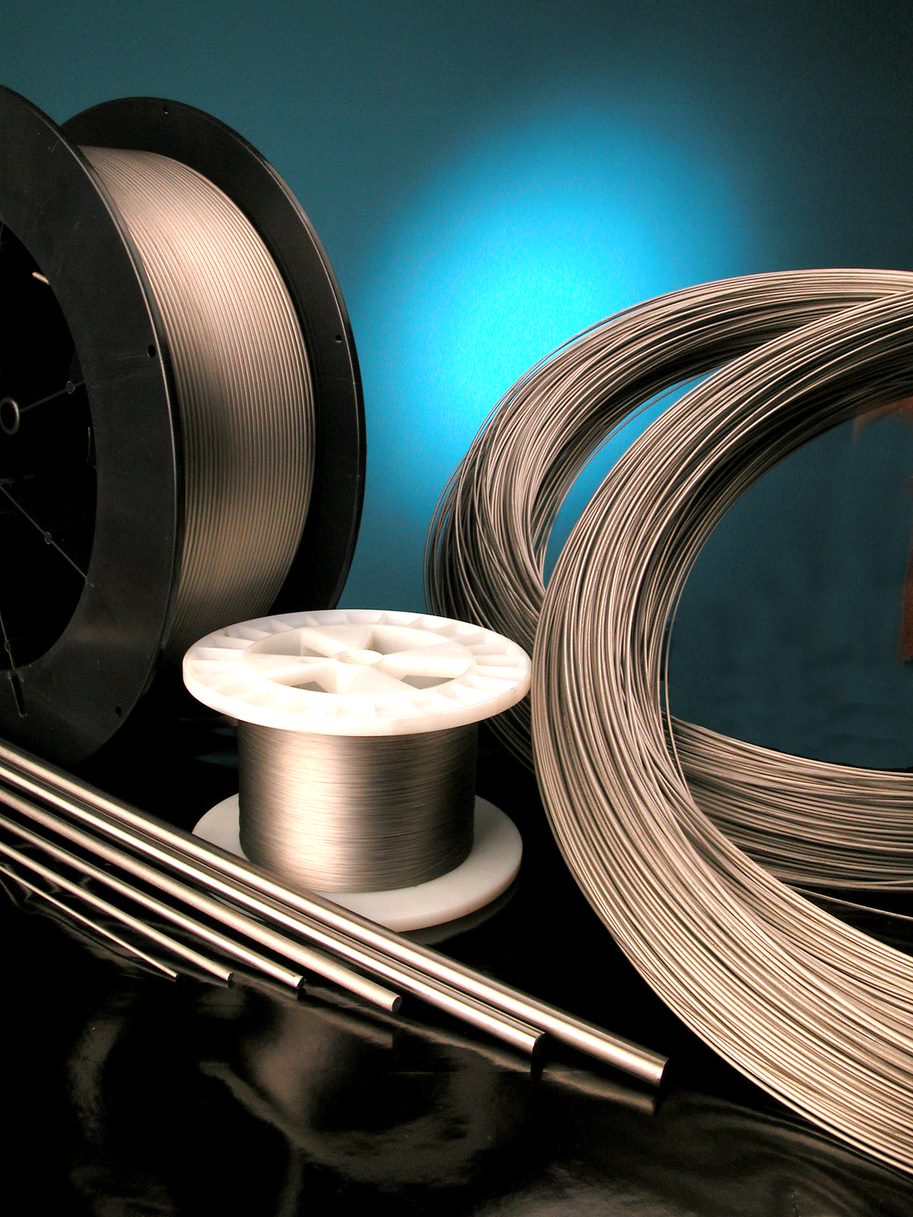
The alloy is melted using Vacuum Induction Melting (VIM) techniques, followed by Vacuum Arc Remelting (VAR), leading to lower inclusion counts and an improved fatigue life. 35N LT® includes less titanium than ATI 35N™ alloy, helping lead wires withstand the functions of the human body for longer. The alloy was modified to increase the fatigue life of pacemaker lead wires from ten years to one hundred years.
Fort Wayne Metals uses ATI’s material to make their DFT® Wire. The outer sheath is made of 35N LT® while the core is designed by Fort Wayne Metals to provide conductivity and resilience. These wire strands are thinner than the diameter of a human hair and are braided together to make an incredibly strong lead wire that is implanted into over 100,000 people a year in the US alone.
At ATI, our markets and applications range from aerospace and defense to medical, meaning that customers can depend on ATI’s proven performance for the body of an engine and the engine of the body. Thanks to the teams at ATI and Fort Wayne Metals, the 35N LT® alloy will keep blood pumping for many years to come.